Additive manufacturing of Ti-alloy: Thermal analysis and assessment of properties
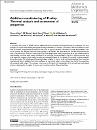
Date
2020-06-01Author
Keles, OmerShuja, S. Z.
Yilbas, Bekir Sami
Al-Qahtani, H.
Hassan, G.
Adesina, A. Y.
Rinaldi, Ali
Khaled, M.
Al-Sharafi, Abdullah
...show more authors ...show less authors
Metadata
Show full item recordAbstract
In this study, 3D printing of Ti6Al4V alloy is realized and the characteristics of the printed layer are examined. The morphological structures and metallurgical changes in the printed layer are assessed. Temperature and stress fields are simulated in line with the experimental conditions. Since the air gaps are present in between the loose alloy powders prior to the printing, the effective properties incorporating the air fraction are determined and the effective properties are used in the simulations. Thermal conductivity of the loose alloy powders with the presence of air gaps is determined by incorporating the virtual experimental technique. It is found that the printed layer is free from micro-cracks and large scale asperities; however, some small pores sites are observed because of the release of air around the loose powders during the printing. Microhardness of the printed surface is higher in the top surface of the printed layer than that of as-received solid alloy. In addition, the friction coefficient of the printed surface remains lower than that of the conventionally produced solid surface. The columnar structures are formed in the mid-section of the printed layer and slanted grains are developed in the region of the top and the bottom surface of the printed layer.
Collections
- Chemistry & Earth Sciences [615 items ]