Experimental analysis and optimization of abrasive waterjet deep hole drilling process parameters for SS AISI 316L
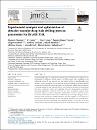
View/ Open
Publisher version (Check access options)
Check access options
Date
2023-09-01Author
Chandar J, BharaniLenin, N.
Kumar, Siva
Gupta, Naveen Kumar
Karthick, Alagar
Suriyan, Rathina
Panchal, Hitesh
Kumar, Abhinav
Patel, Anand
Sadasivuni, Kishor Kumar
...show more authors ...show less authors
Metadata
Show full item recordAbstract
Recent breakthroughs in component downsizing and miniaturization emphasise the requirement for deep-hole drilling with an increased aspect ratio, especially in the automobile sector for fuel injectors and the medical sector for manufacturing bone screws or surgical equipment. In this research, deep hole drilling on stainless steel AISI 316L has been conducted using an Abrasive Waterjet Machine (AWJM), and the influence of drilling variables on the material removal rate, roundness deviation of drilled holes have been evaluated to assess the machining and hole characteristics. In addition, machining parameters’ statistical relevance has been investigated using a multi-parametric analysis of variance. Quadratic mathematical models for material removal rate and roundness deviation have been established by correlating drilling parameters. The Grey Wolf Optimization (GWO) algorithm has been applied in this research to identify the optimal combination of deep hole drilling parameters for maximizing material removal rate and minimizing the roundness deviation. The results have been compared with Derivative-free optimization, Whale optimization, and Harmony search algorithms. The comparison revealed that the GWO algorithm performed better than other algorithms. In addition, a validation test has been carried out to confirm the accuracy of the results produced by the GWO. The images obtained from the scanning electron microscope showed that the surfaces of the deep holes are smooth. Additionally, the ploughing action was shown to be the principal mechanism responsible for removing the material.
Collections
- Center for Advanced Materials Research [1521 items ]