Centrifugal Compressor Spiral Dry Gas Seal Simulation Working at Reverse Rotation
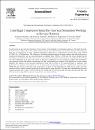
View/ Open
Publisher version (Check access options)
Check access options
Date
2013-11Metadata
Show full item recordAbstract
Unidirectional dry gas seal may experiences reverse rotation when equipped in a centrifugal compressor. This paper describes how the reverse rotation effects on the spiral unidirectional dry gas seal performance and pressure distribution inside the gas film, also an investigation of using a different herringbone shape grooves configurations has been done using ANSYS FLUENT 14.5 CFD simulation. The influence of decreasing rotational speed to the static condition and rotate in the reverse direction on internal flow and gas seal performance is examined from 10800 to -10380rpm. The results indicate that the internal pressure distribution inside the gas seal in reverse rotation is decreased and the open force consequently decreased by 4%. The modification on the same seal is done to enhance its performance at reverse rotation condition. The herringbone spiral grooves is used with different configuration, the new configurations are examined in the forward and reverse rotation direction. The analysis for the pressure distribution is done and its effect on the seal performance is examined. Seal performance is compared with standard one for all geometrical and operating conditions. At high forward rotational speed 10380rpm, the pressure at the end of the spiral groove is about 11.4% higher than the inlet pressure at the seal outer diameter, while at reverse rotation, the pressure is not increased in radial direction. The open force corresponding to reverse rotation increased with a value 1.5kN for both the 100 overlap and 50% forward overlap seal faces, but using seal face with 50% backward overlap failed to enhance the open force at reversal condition.
Collections
- Mechanical & Industrial Engineering [1461 items ]